Elastic Warehouse Part 3: Getting the Elastic Warehouse from the Drawing Board to Reality


Taking the decision to adopt an elastic warehouse approach is probably the biggest decision a logistics company can make in the next 10 years. It sets the path for growth, creates the opportunity to take on larger contracts, differentiate, and perhaps even diversify.
It goes without saying that some companies will need to take a phased approach to implementing the elastic warehouse, moving through the stages of ‘Elastic Overhead’ through to the ‘Elastic Tech’ or ‘Elastic Blend’ model. For those that already have some building blocks in place, they will be able to start with an Elastic Tech model creating a framework that can evolve as demands change and technology develops.
To reiterate from the previous article, the four model approaches to achieving an Elastic Warehouse are:
- Elastic Overheads – making your existing technology, people and warehouse space investments work harder.
- Elastic Outsource – outsourcing warehousing and distribution of key seasonal lines for a finite period.
- Elastic Tech - a complete technology lead implementation.
- Elastic Blend - cherry picking the elements of the first three approaches to give the ultimate financial and operation control.
However, whichever one of the four model approaches are adopted, one of the key components to creating an elastic warehouse is making sure that the physical layout of the warehouse is correctly specified in the first place - using the software to map and understand the best routes, getting the racking laid out in a logical order for goods inward receipting and putaways, bulk storage and quality or quarantine checks areas, through to goods out. Until this is done you cannot effectively optimise your people or teams.
But at whatever point you start, and as with so many strategies, thinking big will be the key to long-term success. Any strategy that adopts the fundamental technological components and has an inherent flexibility to add more functionality and capability over time, will provide the scope to grow and deliver economies of scale. As the strategy delivers and the company becomes more efficient and agile, so it will be better placed to service larger contracts with more complex demands, such as seasonal fluctuations.
Since, most organisations will strive to achieve an Elastic Tech or elements of the Elastic Blend model to provide the ultimate financial and operation control, this paper will the answer the questions the board will ask:
- What are the technology options and how is it possible to design a suitable ‘future-proofed’ infrastructure?
- Does the organisational design need to change?
- Can the investment be spread out over time, and what are the milestones to achieve an ROI?
- What are the internal cost considerations for re-allocation of manpower for example?
- How do we select an implementation specialist we can trust?
- What’s the best practice approach to rolling out the solution and how do we manage the people?
Let’s get technical
Navigating the technology options may seem overwhelming when you first sit down to model your future warehouse facility. However, a little knowledge can go a long way and help to give you focus. This next section sets out some of the technology options and the scenarios they are best suited to.
It’s estimated that 40-60% of warehouse operational costs are absorbed by picking, so it makes sense to focus attention on the process as it’s the area that can deliver the biggest gains and create the most flexibility if made more efficient.
Paper based systems are a thing of the past in the new world of the Elastic Warehouse and it’s easy to see why:
- 45% of picking errors in a paper based system are caused by operators omitting items that are in stock
- 30% of errors are due to the operator picking the wrong item
- 23% of errors are due to a miscount of quantity
- 2% of errors are due to paperwork error
Introducing a Warehouse Management System can help to eradicate many of these issues as it gives a structure and sequence to how things are organised and how they are picked. In effect it controls the whole process of how goods are stored and moved through the operation with every movement monitored and receipted. Though a paper-based system in theory should achieve this, in reality, as those figures show, it doesn’t have the accuracy needed to meet the demands of the supermarket. Utilising automatic identification and data capture technology (AIDC) within the WMS will efficiently monitor and manage the flow of products and data, reducing or eliminating costly errors.
Of course picking is just one application and it is likely that some companies have already made an investment in RF picking. In reality there are many areas where technology integration can be utilised to great effect for example goods in, putaway, packing and dispatch. We should also not forget the opportunities for the wider area warehouse within the Elastic Warehouse structure such as distribution and transport systems including implementation of routing and scheduling, driver behaviour and ePOD technology. The significant investment in picking provides the flexibility, scalability and cost justification in the future to roll this solution out to other areas of the elastic warehouse. Partnering with a trusted technology specialist can take these existing processes and optimise these further.
Where automation and technology can help.
There are three main types of picking technology to choose from, all of which can be integrated with a central work management system that tracks the progress of orders, flags bottlenecks and ensures stock is in place to pick, these are: Radio Frequency Scanning, Voice, or Pick to Light.
Radio Frequency Scanning– this uses handheld scanners with a built-in screen displays. Barcodes are used to identify every SKU in the warehouse. When a SKU is found on an electronic picking list, displayed on the handheld’s screen, then the operator scans the SKU to confirm the item has been found, the display then states the number of items to pick. Each item is scanned into the tote and a new command is triggered when all the items for that part of the pick have been scanned. Goods are scanned at Goods In, Putaway and Picking and scanned on to the wagon at goods out, so are tracked at every stage of their journey through the warehouse and beyond. The Warehouse Management System is automatically updated with every scan, giving operational management the knowledge of what’s in stock and where it is. Stock takes becomes unnecessary as stock amounts are always visible, and reports can be generated at any time, and at any frequency. For example minute by minute, hour by hour, weekly, monthly and yearly.
Voice – Using a headset this technology talks to the operator, telling them where to go, and how many items to pick. In return the operator can tell the device when it is at the right bay and when they have picked the right number of items. It can be integrated with RF Scanning to improve accuracy. It’s a great solution to use where there are multiple languages spoken among the workforce as the language setting can be changed very easily. It also useful where the warehouse operatives needs both hand free to pick individual items, or cartons or has a lot of fine picks. Voice is particularly useful when the operative needs line of sight so is not distracted by looking at a screen, or if the operative is visually impaired.
Both of these options can be adapted to different device form factors from the very small that fit on a finger, to ones that strap to the wrist, to those that can be mounted on a fork lift. It’s really important to consider which type of device best suits the scenario – the wrong device can slow people down and have the reverse effect.
Typically Radio Frequency Scanning is the least expensive of the three technologies, while the hardware for a voice system will cost approximately 70%-120% more than an RF system.
Pick to Light – this uses a light bulb to show a person which bay they should pick from, sometimes integrated with a digital display to say how many items to pick. The bulb goes off when a motion of weight sensor recognises that part of the pick is complete. It’s possible to achieve very high pick rates with Pick to Light but it is best suited to picking small parts such as washers, or screws, and so not considered a suitable option for FMCG retail of food logistics.
Picking Rates
Studies have shown that the following general picking and accuracy rates can be expected for RF, Voice and Pick to Light.
Technology |
Expected Pick Rate |
Accuracy |
RF Scanning |
50-190 lines per hour |
99.3% - 99.5% |
Voice |
175-275 lines per hour |
99.7% - 99.97% |
Pick to Light |
110-350 lines per hour |
99.5% - 99.7% |
It’s well worth investing some time in a little reconnaissance too. There are many companies that will have been in the same situation as you. Following competition law rules, it’s therefore very worthwhile to use your network to go and see similar operations and understand how they use technology, as well as see how they made the transition. A good technology supplier should also be able to help you set up such visits.
By understanding how technology is being used, the processes it supports and the skills and investment needed to make it happen you will find yourself in a better position to create a vision for your company and identify the budgets and potential ROI.
Technology |
Comments |
Typical Cost Advantages |
Migrating from Paper to Proteus Warehouse Using RF Scanning Technology |
Still a common and frequent requirement – many growing organisations have yet to take advantage of this simple adoption of traditional techniques. |
Cost/efficiency savings – up to 25% ROI within 6 – 18 months. Establishes platform for growth while avoiding associated costs by increasing all round efficiency. |
Proteus WMS Voice – Proteus Warehouse Incorporating Voice Controlled Picking |
Now in its second generation, and is cheaper and easier to use than older versions and now being adopted by mid-range organisations with fine picking and multi lingual requirements to improve picking rates and reduce error. |
Cost/efficiency savings – up to 25% over RF ROI within 6 – 18 months. Increases risk speed and reduces cost of error for fast moving fine picking requirements. Particularly effective if foreign workers are employed and for international use. |
Proteus/TouchStar ‘Modulus’ - New Scanning Technologies |
New concept using an ultra tough modular central chassis to bolt-on task specific components. Avoids repair costs and increases versatility. |
Cost/efficiency savings – up to 30% of traditional scanner lifetime costs Lower breakage rates, hardware re-used for different applications. |
Proteus Cloud ERP/ Accounting and Warehousing Solutions |
A hosted version of our industry strength software suite ideally suited to those enterprises who wish to implement quickly, minimise internal IT costs and capital outlay. |
Cost/efficiency savings – up to 50% Avoids large up front, capital outlay, internal IT costs, hardware upgrade costs. |
People power
The board’s commitment to the programme is absolutely essential to ensure success. Its ability to explain the vision to every individual in a positive and concise way will go a long way to make the early days of being an Elastic warehouse run smoothly.
Of course, turning the vision into reality is an enormous challenge and one that will warrant a great deal of change for people. A new organisational blueprint must therefore be drawn up to support the new technical design. It must be validated and agreed before it is evangelised, or risk alienating people.
The best blueprints are done in tandem with the infrastructure design, as how things are done informs when it is done and by whom it is done. In effect, a full process chain is created from which a technical architecture and skills matrix can be created.
Not only will this simultaneous approach ensure the technology is adopted and used to its full potential, but it allays the fears that people may have about job security for example. If the job roles are specified and the benefits are clearly defined and supported by full technical training, then the uncertainty wanes. People see their role in the future organisation and can see how the changes will make improvements to their working day and their abiility to achieve more and fulfill their own potential.
Many organisations find that it is helpful to include members of the team in the planning. While a management team should be appointed to oversee the programme, it should not be underestimated the value of including the people who will be most effected. Their experience knowledge can often offer the nuggets of information that make or break an implementation.
They can assist with:
- Identifying ‘broken’ or laboured processes that technology can fix
- Helping to map out best practice processes
- Assisting with technology trials and refinements
- Acting as technology champions who galvanise people into adopting the strategy
- Train the trainer programmes
Taking an inclusive approach often helps management teams identify the intricacies and nuances that could otherwise have been overlooked. This helps to avoid false starts when the Elastic Warehouse launches, especially if it is supported by a trusted and knowledgeable third party. Selecting that party is as critical as selecting the right technology and getting the blueprint right.
So who should you work with to make it happen?
A well structured Elastic Warehouse programme will start off with a tender process, responding to a detailed brief and culminating in the evaluation of bids according to the technology solutions recommended and the cost.
A bid process can be complex to manage, and the decision making process even more so. A sensible way to organise the information is to use a scorecard, where by the ability to meet specific requirements criteria is given a rating. When the individual scores are totaled together a very clear picture is drawn.
However, as with so many successful implementations, the success will not just come down to the technology selected but the people who deliver it for you. It’s inevitable you will need to work with a third party to make the strategy a reality. Much of this success will rest on how well the supplier gets to know your business, your strategy and the industry you service. So while a scorecard can give you some of the answers, it’s important to evaluate the supplier relationship. Many organisations find it useful to think about how their own values are reflected in the companies they do business with.
A check list of considerations includes:
- How well do they understand our business, the issues we face and must manage, and those we want to eradicate, or perhaps even those we anticipate will need to be accommodated as legislation changes? Do they understand what the future will look like including the changing face of customer requirements?
- Can they provide a solution that has scale and will help us anticipate changing demands? How will they support us in the great task of getting our people ready for the change?
- How prepared are they to help us protect our existing investments and legacy systems? Can they help us set the right pace of change?
- What past implementations have they done that we can learn from – how smoothly did they go, do their customers rate them? Recommendations speak volumes and can give you the confidence you are making the right choices.
- How will they use their experience to inform our business case and maximise our ROI in the shortest time possible without cutting corners or putting long term success at risk?
- Will they give us competitive advantage, drive out errors, and support us after the implementation to ensure we maximise the potential of our investment on the most economical terms?
- Will they ensure business continuity and SLAs are met during the change?
Embarking on a program of change comes with many challenges. Understanding the pitfalls and planning to manage them is a critical part of the Elastic Warehouse puzzle. Get the balance between technology, people and supplier right and the rewards can be great.
Companies must understand their own processes, work on them and document the findings before any creation of the elastic warehouse can begin. This is generally the key sticking point which holds up most technology implementations and is often the area where advice from a technology provider is key to help understand:
- how a company currently operates
- how it should operate
- what do they want to improve?
- what are the technologies that will help them improve?
Want more like this?
Want more like this?
Insight delivered to your inbox
Keep up to date with our free email. Hand picked whitepapers and posts from our blog, as well as exclusive videos and webinar invitations keep our Users one step ahead.
By clicking 'SIGN UP', you agree to our Terms of Use and Privacy Policy
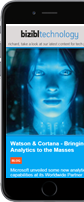
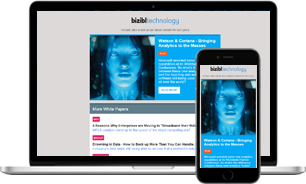
By clicking 'SIGN UP', you agree to our Terms of Use and Privacy Policy
Other content you may be interested in
Categories

Want more like this?
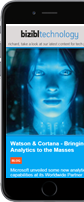
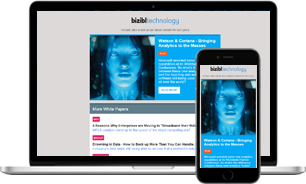
Want more like this?
Insight delivered to your inbox
Keep up to date with our free email. Hand picked whitepapers and posts from our blog, as well as exclusive videos and webinar invitations keep our Users one step ahead.
By clicking 'SIGN UP', you agree to our Terms of Use and Privacy Policy